Executive Summary:
Our Spring ‘23 conference, “Creative Disruption? Innovations in Supply Chain Management,” highlighted the challenges and opportunities faced by global supply chains in the wake of unprecedented disruptions. Speakers from academia and industry discussed such themes as the balance between efficiency and resilience, the role of advanced technologies in modernizing supply chains, workforce issues, and (de)globalization.
Here are the key findings from the report:
- Efficiency-Resilience Dilemma: The conference discussed the tension between optimizing for efficiency and preparing for disruptions in supply chains. Toyota’s lean production and Just-In-Time (JIT) approaches were developed to reconcile efficiency and resilience via learning processes triggered by low slack. But many adopters focused just on efficiency and disregarded the necessity of learning through continual problem-solving that builds capabilities. In the aftermath of the pandemic, the pendulum swung towards a particular approach to resilience – “Just-in-Case” – which carries its own risks by threatening a firm’s long-term competitiveness.
- Just-In-Time vs. “Just-in-Case”: Just-in-time (JIT) supply chains focus on synchronizing supplies and production with customer demand to reduce costs and improve efficiency. Minimal slack, in the form of low inventories, makes minor production and supply disruptions unavoidable. But when those are viewed through a learning lens, they become opportunities to hone recovery capabilities, test emergency plans and strengthen relationships with suppliers in preparation for major disruptions. As Prof. John Paul MacDuffie noted, few managers revisit these fundamental ideas behind JIT today. Instead, they strive to ensure resilience by maximizing their inventories and other buffers “just-in-case” (JIC). Prof. MacDuffie argued against this and proposed a Supply Chain Continuation Capabilities (SCCC) model that maintains the principles of JIT and lean production but adapts them to major crises which the Toyota System’s founders did not anticipate.
- Building Modern Supply Chains: Connectedness and transparency for up-to-date information from suppliers at all tiers plus a system-wide perspective emerged as crucial factors in modern supply chains. Integration and collaboration among supply chain entities, including suppliers, manufacturers, distributors, and customers, were highlighted as key to success. Leveraging advanced technologies such as IoT devices, data analytics, and integrated systems can improve real-time data capture, analysis and sharing, enabling agile decision-making.
- Understanding Workforce Issues: Several speakers emphasized the significance of addressing workforce challenges in supply chain management. Siloed information and limited insight across the organization were identified as obstacles. Digitizing employees’ expertise and knowledge, providing comprehensive training, and promoting innovative thinking were suggested as strategies to enhance agility and overcome workforce-related limitations.
- Navigating Customized Goods Through Supply Chains: The growing demand for customized and personalized consumer goods simplifies just-in-time delivery but increases the complexity of supply chains. Retailers exercise more control over the schedule for delivering custom orders, reduce the stock of generic goods in their warehouses and showrooms, and offer more predictability to their suppliers. At the same time, the specificity of products and supplies needed at each time point introduces more complexity in supply chains. Companies are still learning how to navigate this tradeoff.
- (De)Globalization: Global instability has led many firms to explore alternatives to offshoring, such as reshoring, nearshoring, and friendshoring. The conference participants compared these alternatives and concluded that none of them is satisfactory on its own. Prof. Gad Allon noted that “friendship” with immediate suppliers does not guarantee that “enemies” do not appear upstream the supply chain as a whole. As growing consumer awareness and advocacy are leading to a stronger focus on ethical and sustainable supply chains, firms deal with an ever-increasing number of supply chain parameters which academics should help them optimize.
Introduction
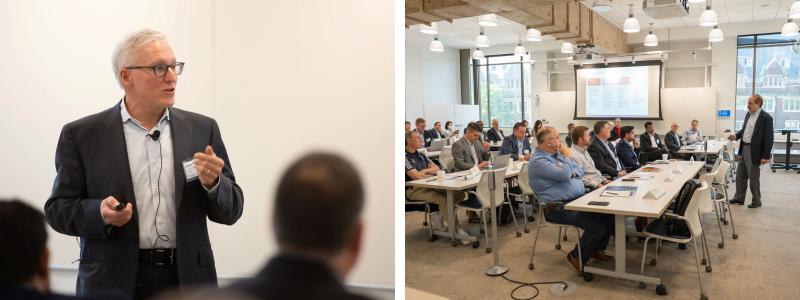
Rethinking Supply Chains Post-COVID
The past three years have seen unprecedented disruptions to global supply chains. The COVID-19 pandemic, the war in Ukraine, rising tensions with China, and climate change have caused shocks, shortages and volatility, calling into question the resilience of our supply chains.
In addition to their short-term effects on the market, these disruptions have challenged basic assumptions undergirding much of the thinking about supply chains. More people are questioning the widespread practice of optimizing efficiency over crisis preparation and calling for a long-term shift towards emphasizing resilience. Some have argued that the effects of COVID in particular have laid bare the essential fragility of our supply chains, and that de-emphasizing efficiency (and thus profit) is the only way to avoid disaster.
At the same time, new technologies like artificial intelligence, machine learning and cloud computing are poised to transform supply chain management. These technologies offer unprecedented opportunities to enhance operational efficiency, optimize decision-making, and drive innovation throughout the supply chain ecosystem.
Historically, supply chains may have been thought of as unproblematic, but recent events have thrust the issue into the spotlight: “Fifteen years ago, few wanted to talk about supply chain risk,” said Simon Sølvsten, Head of Organizational Resilience Research at Willis Towers Watson. “Now, everyone does. Everything must be linked to supply chain, whether it’s AI or risk optimization.”
While sometimes neglected by industry, supply chains have long been a research topic for academics. At Wharton, professors Gad Allon, Hamsa Bastani, Morris Cohen, Marshall Fisher, John Paul MacDuffie, and others have done groundbreaking research into the subject, some of which is funded by the Mack Institute. Our Spring ‘23 Conference became a venue for learning from this research and shaping its future agenda in close interactions with representatives from the industries navigating this turbulent time.
Theme 1: The Efficiency-Resilience Dilemma
Striking A Balance
A major theme of the conference was the reevaluation of the efficiency-resilience dilemma, the well-established idea that there is tension between optimizing supply chains for efficiency and preparing for disruptions. Historically, Toyota’s inventions of lean production and just-in-time delivery have dominated supply chain management.
The post-pandemic debate presented Toyota’s inventions almost exclusively as a tool for reducing waste, enhancing productivity, and thus optimizing for efficiency. Some argued that following Toyota’s approach leaves supply chains vulnerable to disruptions. The shock of the pandemic’s impact on supply chains led to a shift in mindset within many industries, driven by the argument that we need to re-emphasize resilience, even if it comes at the expense of efficiency.
John Paul MacDuffie, Wharton Professor of Management and Director of the Mack Institute’s Program on Vehicle and Mobility Innovation (PVMI) reminded participants that the dominant view of the Toyota System described above is incomplete because it forgets how, at its core, Toyota’s approach is designed to maximize learning. By minimizing inventory levels, supply chain managers achieve more than efficiency. They make production vulnerable to minor interruptions which firms handle via learning processes and routines for problem-solving – and they similarly make supply chains vulnerable to minor disruptions which firms handle in close collaboration with their suppliers. By doing so, they build stronger knowledge of their own operations while also strengthening their relationships with suppliers, both of which help in preparing for totally unanticipated disruptions. While some industry practitioners see single- or dual-source suppliers as a problem for resilience, arguing for having a larger set of suppliers “just-in-case”, having fewer supplier relationships can be a major part of the solution if the buyer treats them as long-term partners rather than transactional market counterparts.
Prof. MacDuffie also cautioned against the hypervigilance that has led some firms to de-emphasize efficiency.
“Yes, COVID was extraordinary,” he said. “But it was also ordinary, because supply chains are always being disrupted. I won’t deny that there’s a trade-off between efficiency and resilience. But framing the issue in terms of choosing one or the other is untenable. Disasters hit some firms on some days, but competitive pressures hit all firms every day. If you make a lot of adaptations to disasters that are by nature unpredictable, you will make mistakes in terms of future competitiveness.”
“Just-In-Time” vs. “Just-in-Case”
MacDuffie drew on his extensive study of the Toyota Production System (TPS) that includes Just-In-Time (JIT) manufacturing as a major component. Developed in the 50s and 60s by Toyota engineers, JIT sought to synchronize production with customer demand, enabling Toyota to reduce inventory and associated costs. Its success at Toyota led to its widespread adoption across industries globally, as organizations recognized the benefits of reduced costs, improved efficiency, and streamlined operations associated with JIT supply chains.
Today’s reaction to JIT is best characterized as “Just-in-Case” (JIC), an exclusive focus on building resilience via maintaining higher inventory levels and adding extra suppliers to address unexpected events and ensure continuity of supply. These strategies gained particular attention in industries with high demand volatility, long lead times, or where the cost of stockouts was significant.
However, MacDuffie urged attendees to reject the false juxtaposition of JIT versus JIC.
“The most successful companies manage their supply chain via honing daily operations and planning proactively,“ he argued. “Working on small challenges gets you ready for big challenges, and working on big challenges gets you ready for new and unexpected challenges, like COVID. This is the learning philosophy behind TPS that companies tend to forget.”
A New Model: Supply Chain Continuation Capabilities (SCCC)
MacDuffie’s proposed solution is a model developed with Takahiro Fujimoto from the University of Tokyo and Daniel Arturo Heller from Chuo University. Based on the crisis response protocols of Toyota and several other Japanese firms, MacDuffie notes that Supply Chain Continuation Capabilities (SCCC) allows firms to “change flexibly and quickly between a competitiveness-first focus in ‘normal’ times to a continuity-first focus amid a disaster.”
SCCC is based on three complementary principles:
Protective: Minimize damage to facilities and supply chain routes during a crisis. Protective protocols must be developed both proactively (in anticipation of a crisis) and to prevent further damage during a crisis.
Recovery: Execute recoveries quickly and safely after damage caused by a disaster. Strong recovery protocols require knowledgeable advance diagnosis teams, on-the-spot estimation of resources, and real-time adaptive revision.
Substitution: Complement on-the-spot recovery capability after damage from disaster, allowing you to replace damaged sources or sites with an equivalent. However, proper substitution requires advance knowledge and development of potential alternate sources or sites.
Read more about Supply Chain Continuation Capabilities (SCCC) in the working paper here.
Theme 2: Building Modern Supply Chains
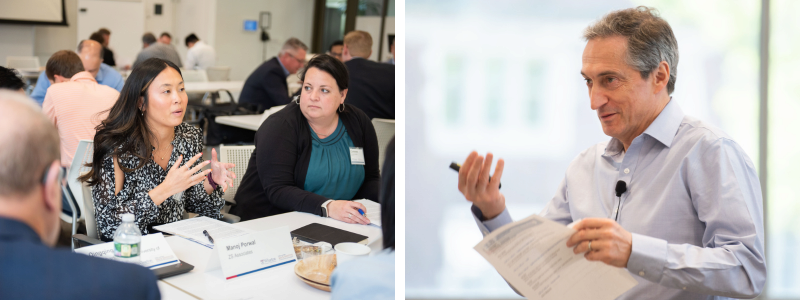
Connectedness and Transparency
Two of the hallmarks of a successful, modern supply chain are connectedness and transparency. A well-connected supply chain has a high level of integration and collaboration among the various entities within the supply chain network, including suppliers, manufacturers, distributors, and customers. Likewise, a successful supply chain has a high level of visibility, allowing firms to easily obtain real-time information about the movement and performance of goods and materials across the network.
Improving these metrics requires firms to leverage advanced technologies such as IoT devices, data analytics, and integrated systems to capture, analyze, and share real-time data from multiple sources throughout the network. These tools allow you to use data to respond to challenges in the moment, as opposed to the old model of collecting large amounts of data and analyzing it at a later date.
“The goal is to stop looking in your rearview mirror,” said Rakesh Gandhi, Vice President of Digital Supply Chain – Industry 4.0 at SAP. “Use data to make decisions in real time.”
“Obtaining visibility requires more than mere words,” he added. “It requires collecting data from various layers of the enterprise, such as design, purchasing, planning, manufacturing, and maintenance operations. It’s essential to gather data not only from the enterprise layer but also from the field and plant, utilizing sensors and PLCs. Contextualizing this data is crucial—that’s how you become truly resilient.”
A Hidden Challenge: Workforce Issues
While the role of technology in improving supply chain visibility is crucial, experts at our conference also frequently brought up the issue of workforce and labor. At the firm level, information about supply chains tends to be siloed, leading to a lack of insight and preparedness across the organization.
“One of the biggest issues in the U.S. impacting supply chain is talent, especially as more people retire,” explained Gandhi. “For many firms, a lot of the most important information in operations and manufacturing is being held in Excel spreadsheets accessed by a few people. The question is: how do you digitize your employees’ expertise and knowledge?”
Susan Helper, Professor of Economics at Case Western University and Senior Advisor for Industrial Strategy at the White House Office of Management and Budget, also spoke of the importance of training workers to think about and understand supply chain issues.
“Your workforce is really important for improving agility,” she said. “We need a long-term focus on providing comprehensive and general training. For example, registered apprenticeships could give people experience in thinking through unusual supply chain disruptions and coming up with creative solutions.”
Speakers stressed that the ultimate goals of any supply chain, in terms of both personnel and technology, are to avoid silos and create an environment where information is relayed in real time and in such a way that insights can be gleaned.
Complex Goods, Complex Supply Chains
Consumer goods of all sorts are becoming more complex and personalized. No longer do identical items roll off the assembly line and onto store shelves. Increasingly, customers expect goods tailored for their needs – a change facilitated by the rise of ecommerce and digitalization.
“You’re dealing with new expectations from customers,” explained Gandhi. “It’s not just about mass manufacturing. If you look at car companies, for example, customers don’t just want a generic SUV. They want it configured to their needs, down to the color and design of the seats.”
This has led to a contradiction in supply chain management. On one hand, increased personalization allows you to do more with less inventory. For example, a retailer selling furniture no longer needs to focus exclusively on the stock in the storeroom. Instead, customers can view samples in a showroom and then order a custom sofa exactly to their liking, using a tablet or even a phone to choose their preferred size, color, and material. Digitalization has allowed this model to gain popularity in industries from automotive to fashion. However, these increasingly complex goods can be hard to source, and may complicate supply chains even as they ease inventory pressures.
“Even when aiming to make the supply chain more customer-friendly, it can inadvertently introduce additional complexity,” said Sølvsten. “There’s a balance that must be struck between risk and customizability.”
Kevin Austin, Group VP for Demand and Supply Management and Supply Chain Transformation at Toyota North America, also spoke about the duality between risk and customizability. Famously, Toyota’s just-in-time system preaches “zero inventory,” a model that Austin says the automotive giant is working hard to digitize with the customizability model discussed above.
“There’s pros and cons to low inventory,” he said. “Some customers are more willing to wait as long as it takes to get a car exactly to their specifications, which makes supply chains more stable and predictable. But it creates new challenges as well. The traditional, analog ways of managing inventory need to catch up to the digital customization model.”
According to Austin, Toyota is shifting towards a model that allows for individual customization of each vehicle sold, fundamentally reshaping the role of the supply chain within the company.
“In our organization, supply chain has always been viewed as a utility, like electricity or water. You’ve got to have utilities but there’s nothing exciting or extra about them,” he said. “And so, what we’ve been trying to do is to change that paradigm by putting the customer right in the center of the supply chain and designing the supply chain around the customer.”
One unexpected insight that the move towards digitized customization has provided to Austin is a rethinking of the concept of supply and demand.
“We used to think that the cars that were sold represented customer demand. But, often, it’s the customer buying whatever is available. The digital products we’re building allow us to capture customers’ first choices and any approved substitutions. That gives us new insight through data. What did customers initially want? What substitutes do they prefer? Think of the power in how that will allow us to spec our products for the future.”
Theme 3: Calculating and Understanding Risk
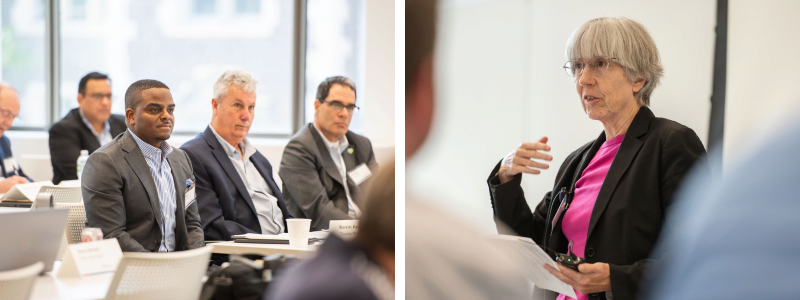
Moving Beyond COVID
Simon Sølvsten, Head of Organizational Resilience Research at Willis Towers Watson, shared insights from WTW’s 2023 Global Supply Chain Risk Report, which interviewed 800 industry decision makers from key sectors, from food and beverage to semiconductors. One of the study’s findings was that firms tended to overestimate certain risks to supply chains while underestimating the impact of other factors.
“People tend to be biased towards what they’ve most recently experienced,” said Sølvsten. “They might also be biased by internal data that only tells part of the story and are frequently highly influenced by the media.”
For example, firms are often fixated on COVID and extreme weather events, when such events are comparatively rare.
“When do we see frequent payouts from insurance coverage?” he asked. “It’s not because of tsunamis or pandemics. It’s more likely to be factory fires that stop the supply chain. But we rarely talk about them. Everywhere I go, people talk about the pandemic. Of course, we need to prepare for another pandemic. But what about fire? That’s something that could happen to almost anyone, in any foreseeable future.”
Gad Allon, Professor of Operations, Information and Decisions, also urged firms to think beyond COVID. Like MacDuffie and Sølvsten, he worried that the renewed attention to supply chain resilience is backward-looking, and that firms are not truly prepared for challenges they are likely to face.
“So many of the solutions I hear for supply chains are geared still at solving the pandemic issue,” he warned. “We’re building a supply chain to address an event that has already occurred. COVID won’t happen again, but the challenges and disruptions undergirding it will continue to happen—let’s prepare for those.”
Climate Change
While Sølvsten encourages people not to fixate on unlikely weather events, he also said that climate change is a well-founded concern that is rightfully gaining attention from industry. Rising sea levels, more frequent wildfires, and massive storms do pose a serious threat to supply chains, and are already beginning to impose costs.
“Managers are beginning to express more concern about climate change,” he said. “That’s a risk factor in the global market that we need to carefully consider. We see that the frequency and severities of global climate-change-related catastrophes are increasing. There’s no doubt. And they are disrupting our supply chains more often and with more serious repercussions. This will worse in the future. I’d bet on that.”
Challenges To Risk Analysis
Accurately assessing supply chain risk is a persistent challenge for insurers that leads to a lack of adequate coverage for supply chain managers. For example, during the pandemic, every single major insurance company backed out of its supply chain contracts. While this was an extreme example, it points to a larger problem of quantifying the risk of supply chain disruption. Because supply chains are so fragile and interconnected, one mishap can cause a major derailment. This leads insurers to overestimate gross (overall) risk while not properly taking into account mitigation strategies.
Sølvsten believes that the key to more accurate risk assessment (and, thus, better insurance coverage) is through data-sharing. While firms tend to hold supply chain information close to their chests, he is hopeful that academia can play a role in analyzing and disseminating such information.
“We need more data and we need more collaboration between companies. And that’s extremely difficult, especially when we talk about supply chain, because part of the competitive advantage of owning your own supply chain is restricting the information. But I actually think that’s where the academic community might play a vital role. Academics could harvest and anonymize the data, then return it to industries. That will require long-term industry-academic collaboration, but it could help us build supply chains that are truly resilient.”
Theme 4: Production, Manufacturing, and Governance
Made In America?
Many supply chain managers are also rethinking where goods are made. A range of factors from geopolitical tensions to ethical concerns have prompted many to abandon the practice of seeking the lowest-cost manufacturing destination. Their concerns include rising labor costs, trade tensions, geopolitical uncertainties, intellectual property protection challenges, and a desire to diversify supply chain risk by reducing dependence on a single sourcing country. Additionally, rising consumer consciousness has shifted customer preferences towards sustainably sourced, ethically produced, and socially responsible goods.
Notably, this has not resulted in more goods being made in America. Several speakers brought up the relative dearth of domestic manufacturing initiatives in the U.S., especially compared to places like Europe, China, and India, which all have government-industry consortiums to promote domestically made goods.
Susan Helper explained that reshoring goods often requires rethinking the design of the goods themselves, not merely the supply chains.
“A lot of studies that look at the cost of reshoring of, say, an iPhone don’t take into consideration that the production process is optimized for China,” she said. “If we were going to bring production back home, it would be silly to make it the same way we did in China. We would want to change the design or the production process.
Such redesigns can often be beneficial for the company as a whole. Helper worked on the Obama-approved reshoring initiative of the K’Nex toy company and said that the imperative to redesign led to “innovative new products.”
Jamie Bonini, President of the Toyota Production System Support Center at Toyota North America, took a less optimistic view. He suggests “skill gaps” are a big part of what prevents reshoring initiatives from thriving. Bonini claims even highly educated and well-intentioned people struggle with the realities of creating an efficient system on the ground in North America.
“There’s a huge opportunity to do better,” he said. “If we’re going to reshore things to North America, let’s reshore them right. Let’s build high-performing factories. There’s a lot of potential, but we aren’t there yet, in my experience.”
Nearshoring and Friendshoring
Conference attendees also discussed the topics of nearshoring (moving production closer to home) and friendshoring (moving production to politically allied countries). These two concepts have generated lots of buzz, with U.S. Secretary Treasury Janet Yellen, who coined the term “friendshoring,” calling them the linchpin of President Biden’s trade policy.
But Allon was sharply critical of both nearshoring and friendshoring, arguing that friendshoring is “infeasible” due to the complexity of supply chains. Even if a good was apparently produced in an allied country, he argued, supply chains are so complex that there is an almost certain chance that some component of the good was produced in a hostile country.
“Even if you wanted to buy only from firms in allied countries, if you looked two steps down the supply chain, all bets would be off,” he said.
Fundamentally, Allon feels that friendshoring will increase global divides and negatively impact global safety and security, as well as workers’ quality of life. He also argued it will increase the price of goods. He cited a study that found that an iPhone produced only in U.S. allied countries would cost $2,500, more than twice the current price.
“We’re going to see negative impacts that are correlated with global divisions,” he predicted. “Cybersecurity risks are going to be more correlated across countries that are allied, as well as pandemic and demand shocks. Every supply chain we build will be more fragile because these shocks are going to be correlated.”
Yet Allon also believes these risks are already here. Supply chains are becoming more and more “fragmented” and thus less resilient.
“How do we find strategies that allow us to create both positive short-term ROI and positive long-term ROI?” he asked. “Network flexibility is the way to do that. But that is very hard to create and maintain.”
Government Regulation and ESG
Some speakers also touched on the role of government regulation and, in particular, ESG analysis. An aerospace exeuctive said that while sustainability and ESG assessments will one day be a larger part of sourcing criteria, most firms are not there yet.
“At some point, we will get to a point where there’s enough visibility and connectivity where we can start making greener sourcing decisions,” he said. “But it’s a while away.”
Part of the problem, he explained, is that the current method of calculating ESG impacts—in particular, by fossil fuel emissions—is “challenged” by the complexity of supply chains.
“It’s very difficult to differentiate between Business A and Business B,” he said. “You can’t delineate on the basis of actuals for either the companies themselves or their extended supply chain. Accurate ESG scores for supply chains are a while away.”
Conclusion
The conference gave us insight into the myriad challenges facing supply chain managers, painting a picture of an industry reassessing itself in the aftermath of the coronavirus pandemic. Yet, fundamentally, the takeaway message was one of possibility. The Toyota System and MacDuffie’s Supply Chain Continuity Capabilities model show that it is possible to reconcile efficiency and resilience., Supply chain managers can achieve both through learning processes embedded in daily operations that build and leverage close relationships with suppliers and build capabilities via continuous engagement with everyday challenges.
A second major theme was the need to be proactive. Supply chain managers should not fall victim to reacting to disruptions of the past, but should instead look ahead to the challenges of the future. In particular, while increased geopolitical tensions represent major unknowns, moving supply chains closer to home or to allied countries carry their own risks and may fail to avoid the very problems such moves were intended to address.
Perhaps the greatest source of possibility and optimism for supply chain management is new technology. Machine learning, cloud computing, AI, and IoT are poised to transform supply chains, and managers should focus on leveraging these technologies to increase connectedness and transparency. Furthermore, managers should consider retail trends popularized by ecommerce, such as digitalization and personalization.
“There are reasons to be seriously concerned about the state of our supply chains, but there are also remarkable innovations coming from firms like those who spoke to us today,” concluded Dr. Valery Yakubovich, Executive Director of the Mack Institute. “That’s why maintaining a dialogue across industries and between industry and academia is so important. The Mack Institute will always work to be at the forefront of these conversations.”